The Role of Low-Pressure Pumps in Fuel Injection Systems
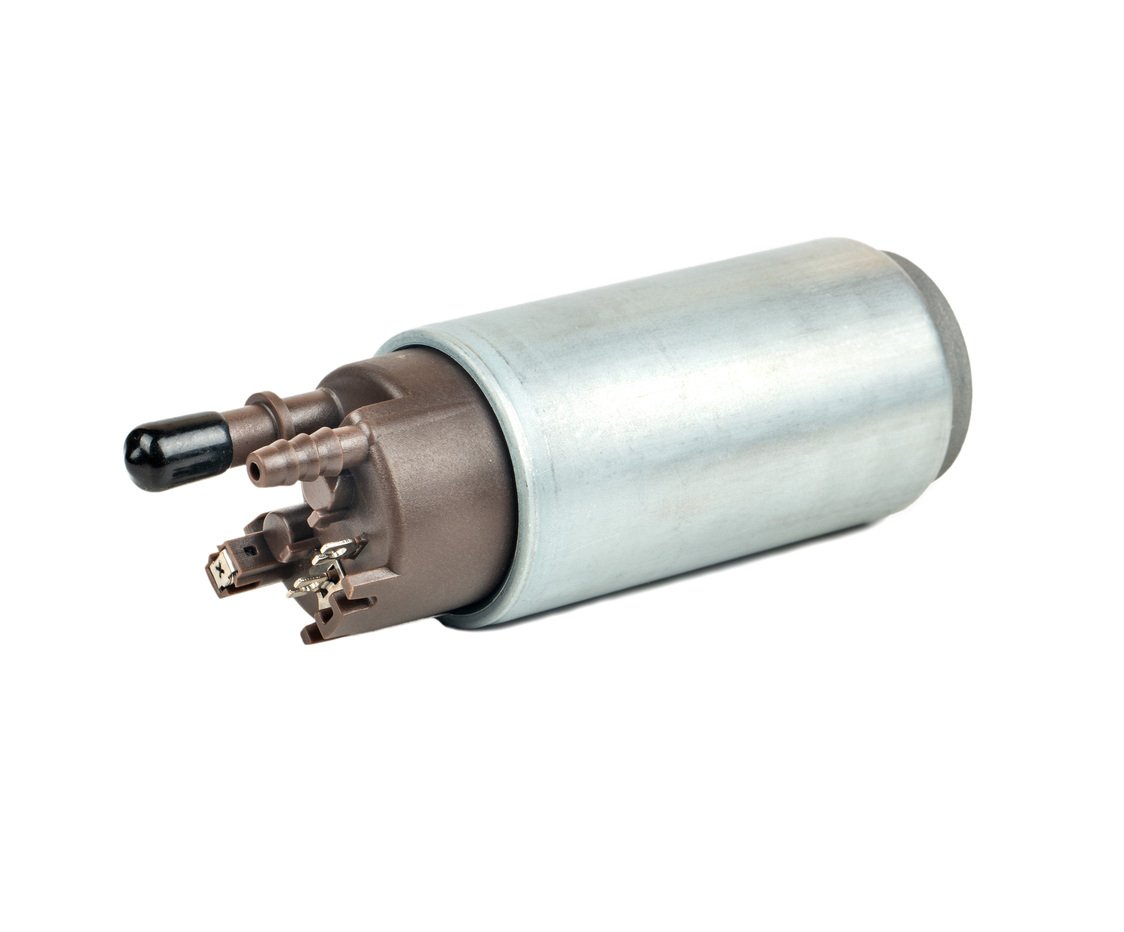
The Role of Low-Pressure Pumps in Fuel Injection Systems
Dec 9, 2024 11:38:09 AM
3
min read
What to Look for in a Gerotor Pump Manufacturer
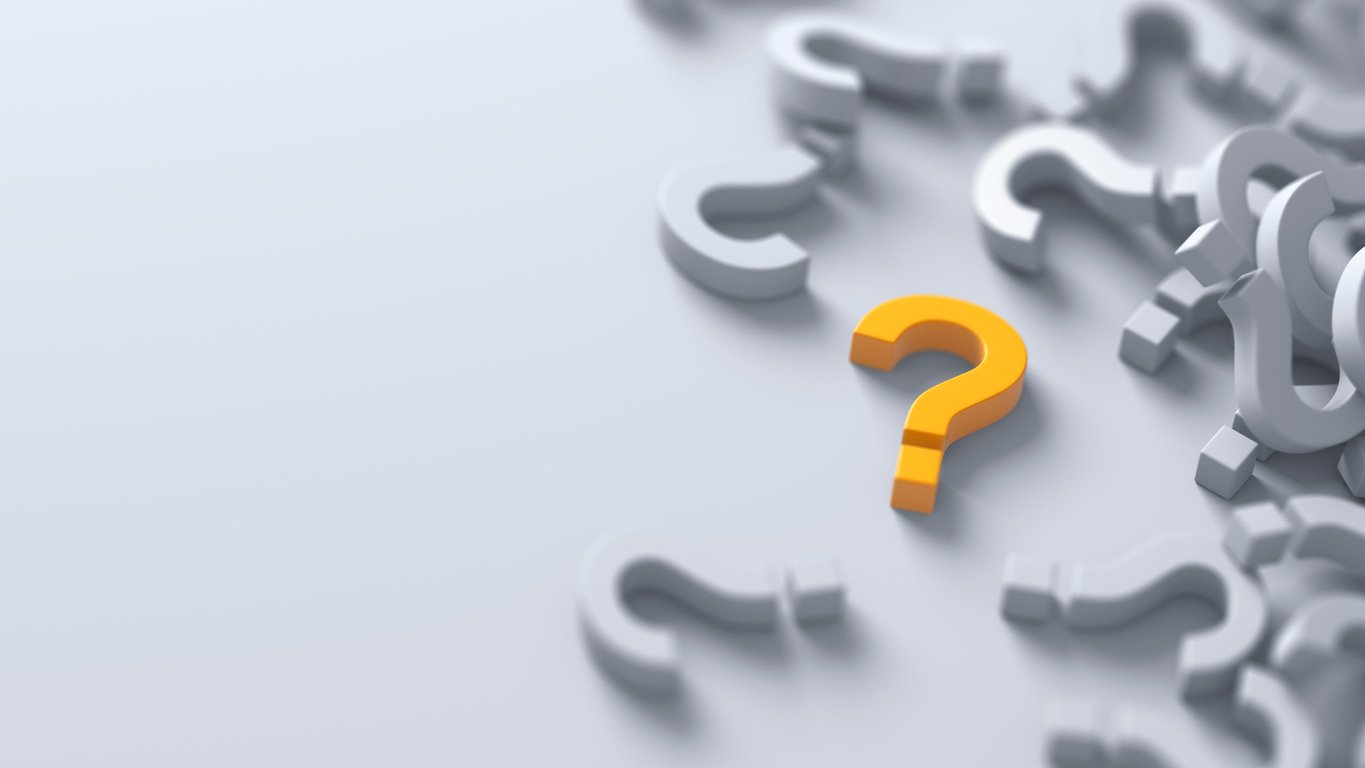
What to Look for in a Gerotor Pump Manufacturer
Dec 9, 2024 11:09:59 AM
3
min read
Advantages & Disadvantages of Mechanically Lubricating Your E-Axle System
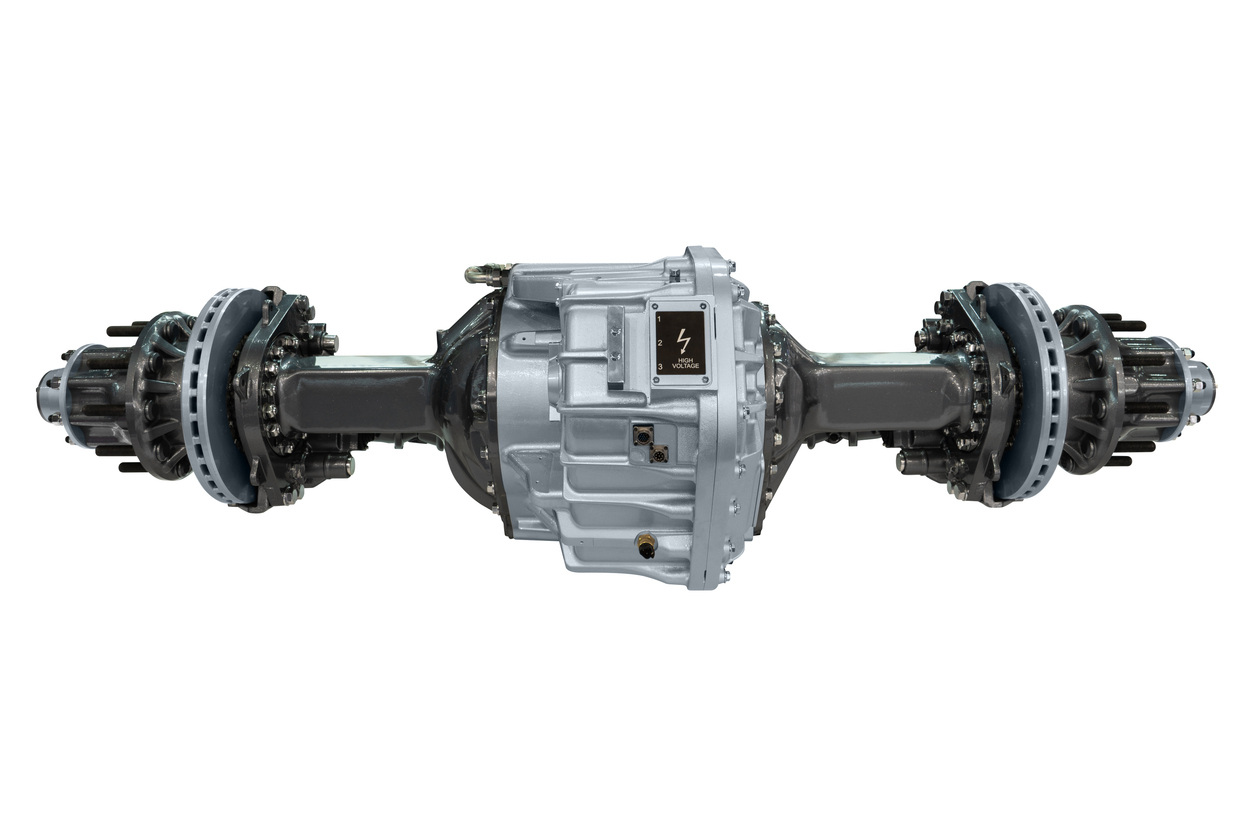
Advantages & Disadvantages of Mechanically Lubricating Your E-Axle System
Dec 9, 2024 10:38:49 AM
5
min read
Mechanical Pumps vs Electric Fuel Pumps: A Comparison
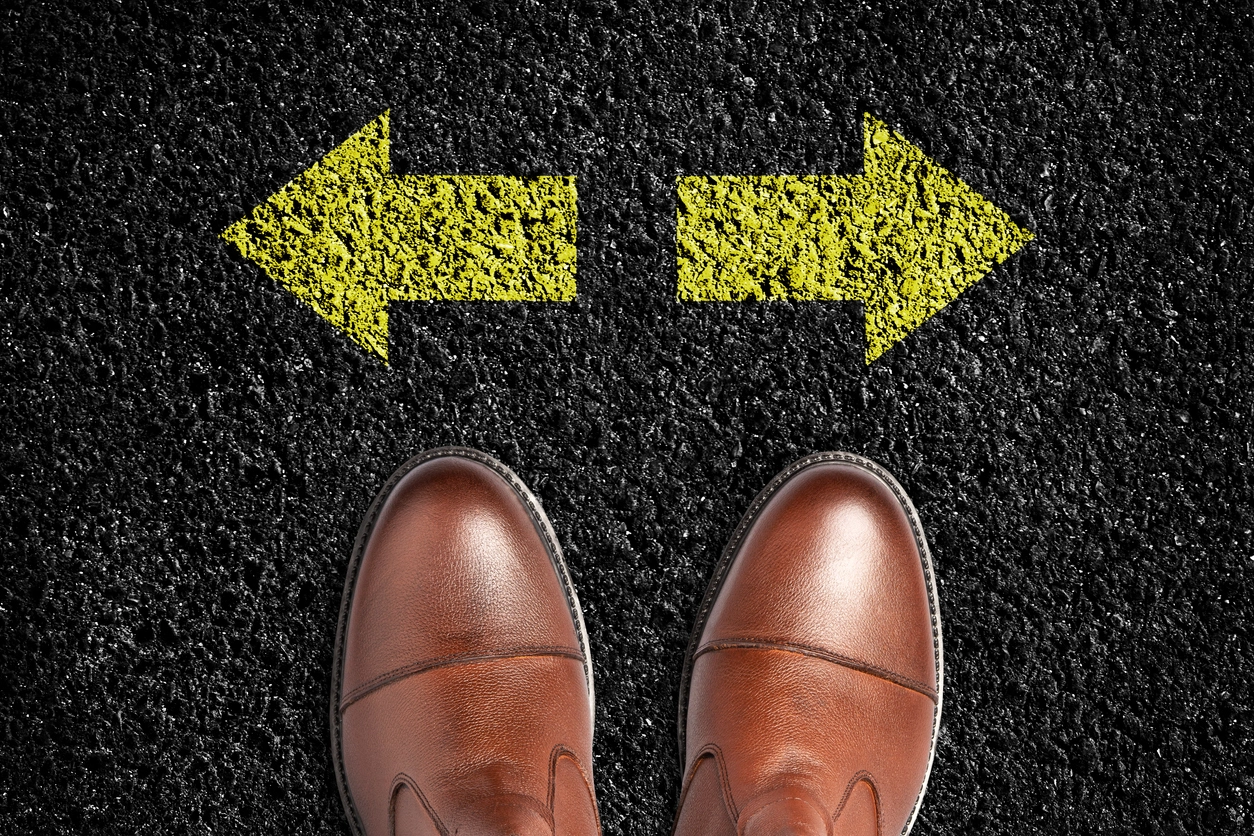
Mechanical Pumps vs Electric Fuel Pumps: A Comparison
May 7, 2024 2:54:09 PM
3
min read
What is a Gerotor Pump? A Comprehensive Overview
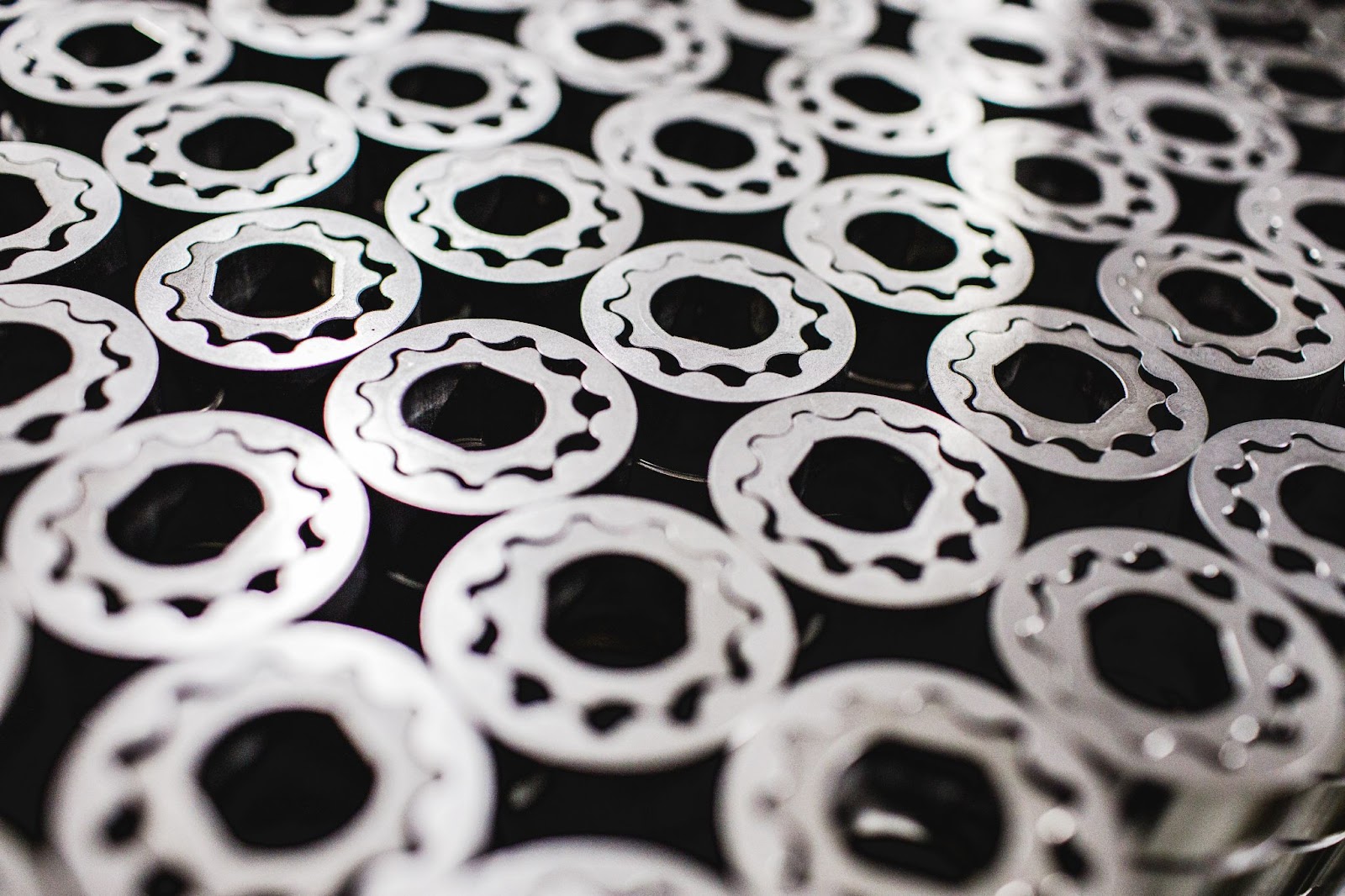
What is a Gerotor Pump? A Comprehensive Overview
Aug 4, 2023 8:35:46 AM
3
min read
Improving Pump Flow Rates & Efficiency
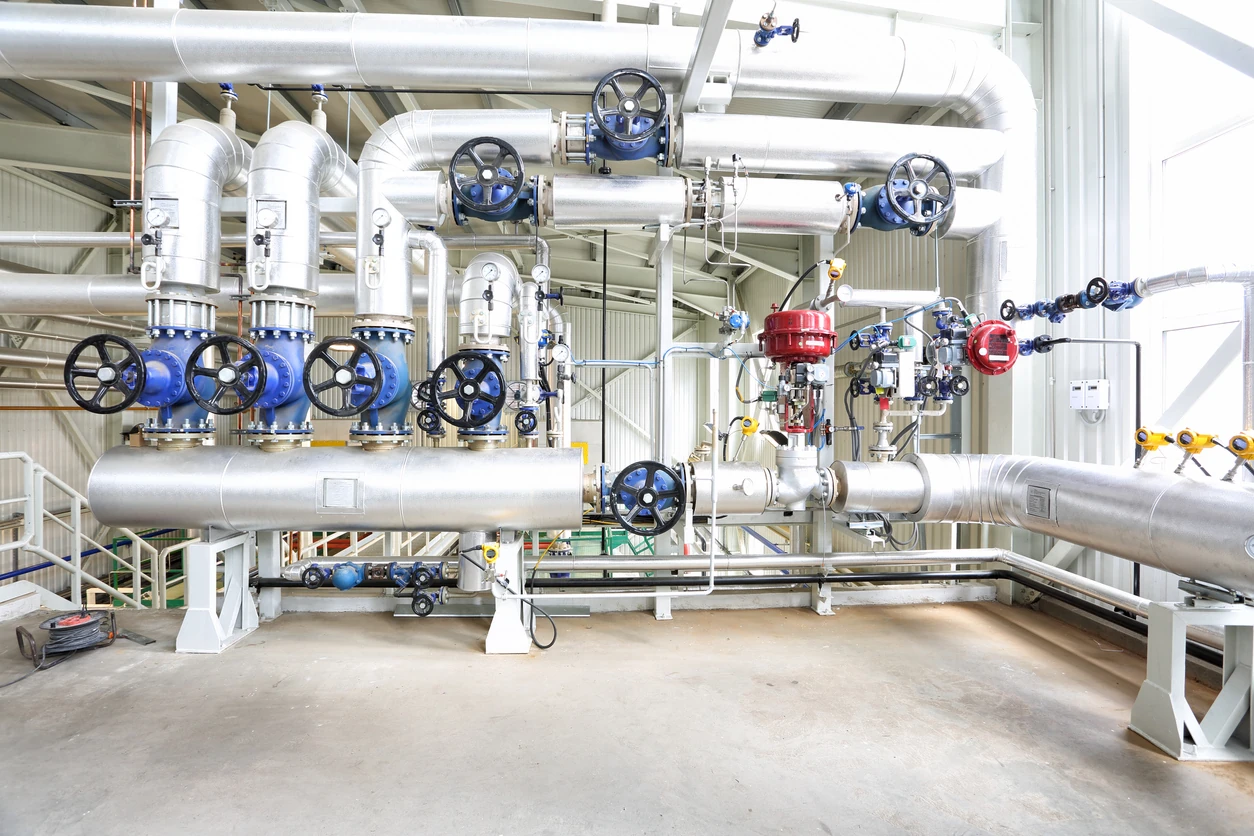
Improving Pump Flow Rates & Efficiency
Aug 3, 2023 11:42:18 AM
4
min read
Sustainable Pump Design: Designing for Recyclability/ Remanufacturing
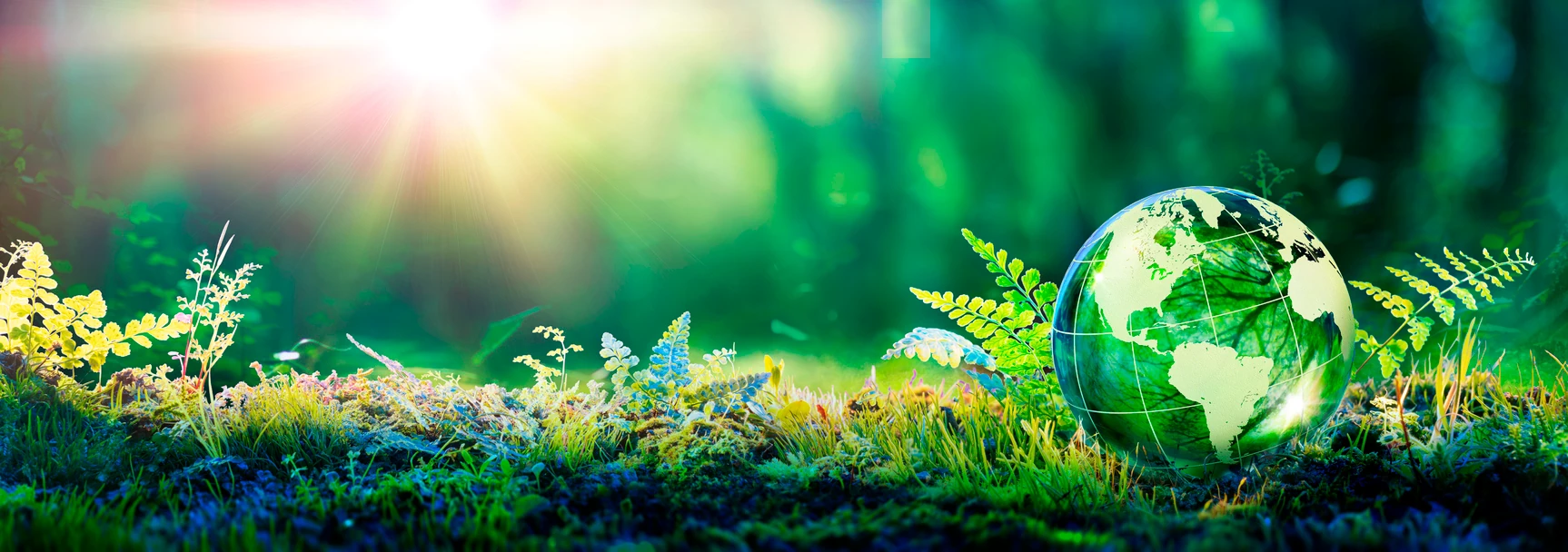
Sustainable Pump Design: Designing for Recyclability/ Remanufacturing
Jul 13, 2023 4:03:02 AM
3
min read
Gerotor Pump Advantages and Disadvantages
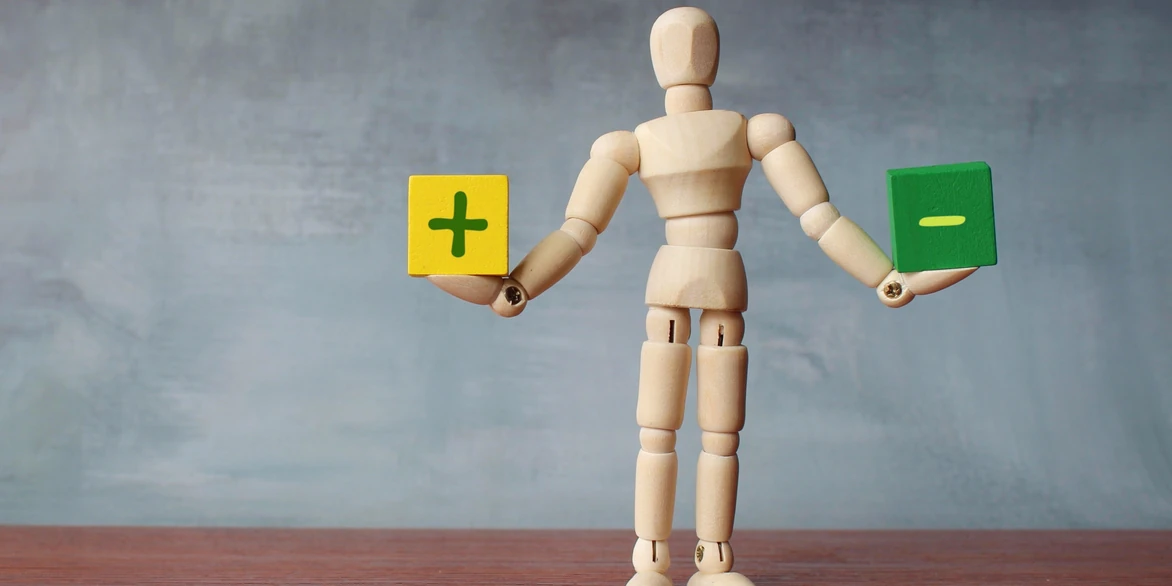
Gerotor Pump Advantages and Disadvantages
Jun 19, 2023 5:38:18 AM
4
min read
Positive Displacement Pump Maintenance: Why Do You Need It?
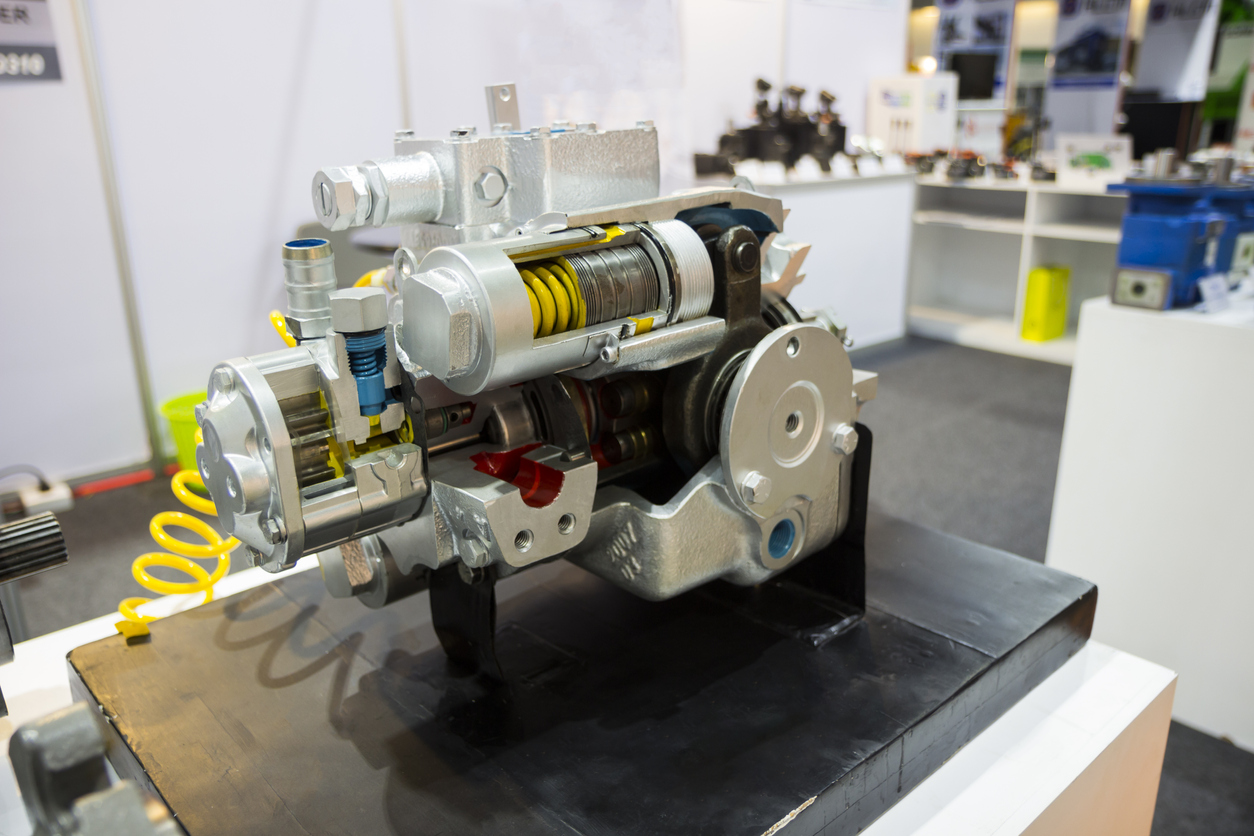
Positive Displacement Pump Maintenance: Why Do You Need It?
Jun 1, 2023 12:16:01 PM
2
min read
The Impact of Viscosity on Positive Displacement Pump Performance
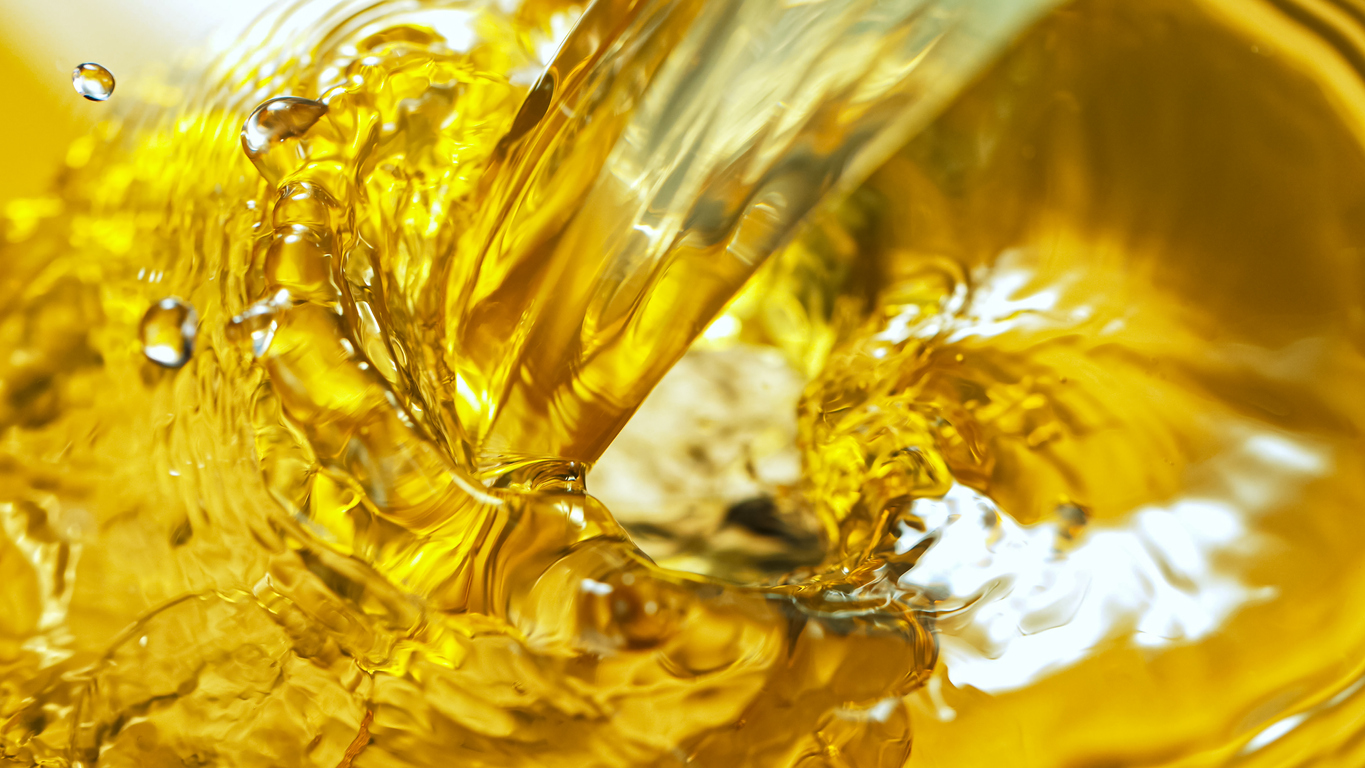
The Impact of Viscosity on Positive Displacement Pump Performance
May 9, 2023 10:01:52 AM
5
min read